Summary: SPH Engineering, based in Latvia, has developed an easy-to-use UAV magnetometer payload with integrated peripherals. The system is available with QTFM in single-sensor and gradiometer configurations.
With the development of compact, low-power, lightweight, and highly sensitive magnetometers like the QTFM, conducting high-resolution surveys of magnetic signatures across large land areas has become increasingly feasible, even with consumer-grade UAVs. Historically, accomplishing such tasks required larger fixed-wing aircraft or helicopters. The range of applications of such aerial surveys is broad, from locating unexploded ordinance and mineral exploration to identifying objects like abandoned oil well heads and power lines, as well as conducting environmental or archaeological surveys.
Equipping UAVs with magnetic sensors often appears as a complex art, requiring careful optimization across several parameters such as UAV selection, sensor mounting techniques, optimal sensor distance from the UAV, and strategies for ground reference sensors, heading error compensation, and synchronization of signals with GPS data. SPH Engineering’s MagNimbus offers an innovative solution to address these complexities for a broad range of applications, enabling users to focus on their specific application without worrying about intricacies of magnetometer science.
MagNimbus utilizes a remarkably simple approach for attaching the sensor to the UAV through a mechanical self-retracting arm. This ingenious design ensures the UAV’s takeoff or landing is unimpeded. Once airborne, the arm extends, distancing the magnetometer from the UAV to reduce interference from its electronic components significantly. The arm’s rigidity prevents the sensor from swaying, addressing numerous potential challenges. This configuration also permits the UAV to operate very close to the ground, significantly magnifying its ability to detect signals from smaller objects.
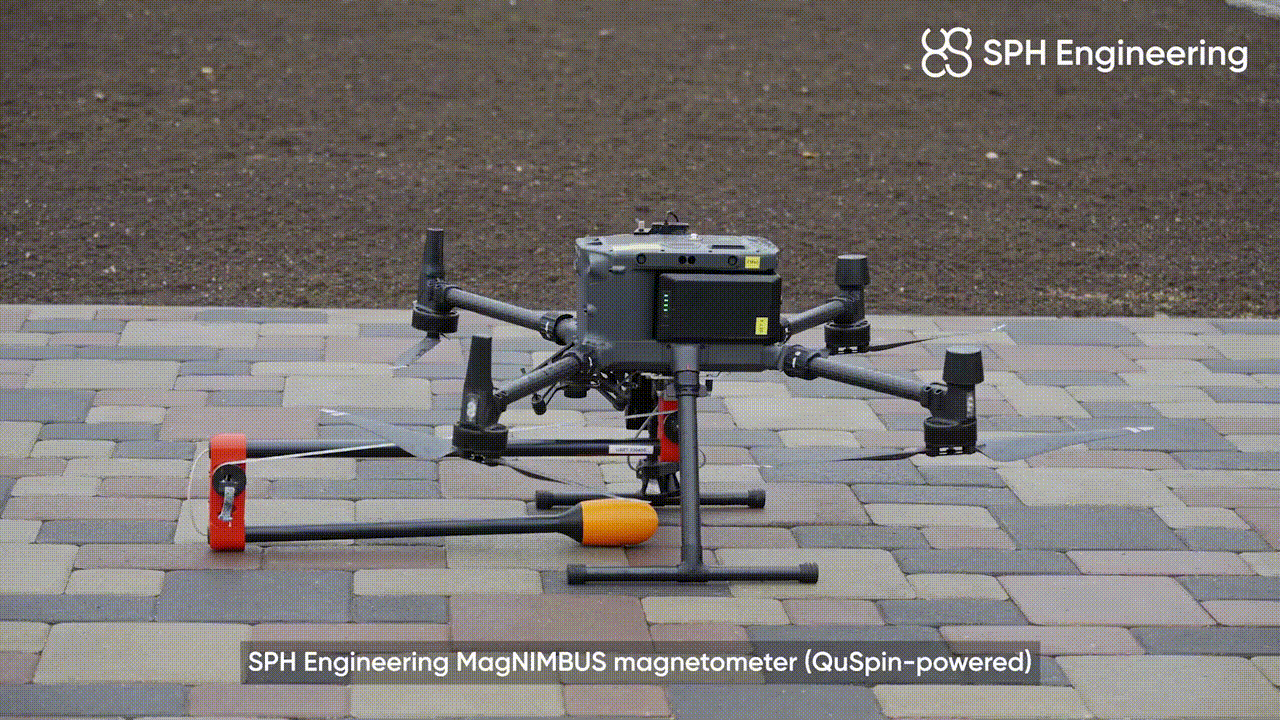