Vector Coil Calibration (For Sensors with Vector Add-On)
Ensure your Gen-2 QTFM sensor’s firmware is updated to version 1_36, released on October 4th, 2024, to support vector coil calibration. If the firmware is outdated, follow the firmware update guide to upgrade before proceeding.
Steps for Vector Coil Calibration:
- Prepare the Sensor:
- Navigate to the ‘Terminal’ tab in the user interface.
- Let the sensor complete autostart and confirm the cell locks. For best calibration results, allow the sensor to run for about 5 minutes before proceeding.
- Verify Sensor Mode and Data Output:
- Ensure the sensor is in vector mode and check that the X, Y, and Z data outputs are valid. This step is crucial to ensure the accuracy of the calibration.
- Initiate and Monitor Calibration:
- Use the ‘Send Decimal’ button to send decimal command ‘6’ to the sensor. You should see a message: “#Calibrating Coil, keep sensor still.” Calibration typically takes 1-2 minutes.
- Once calibration is complete, a status update will display the delta values for each coil, such as “#Delta_X:12040, Delta_Y:6900, Delta_Z:5954”.
- Lock Calibration Values:
- To permanently store the new calibration values, use the ‘Send Decimal’ button to send command ‘9’. This final step updates the internal memory with the newly calibrated vector coil values.
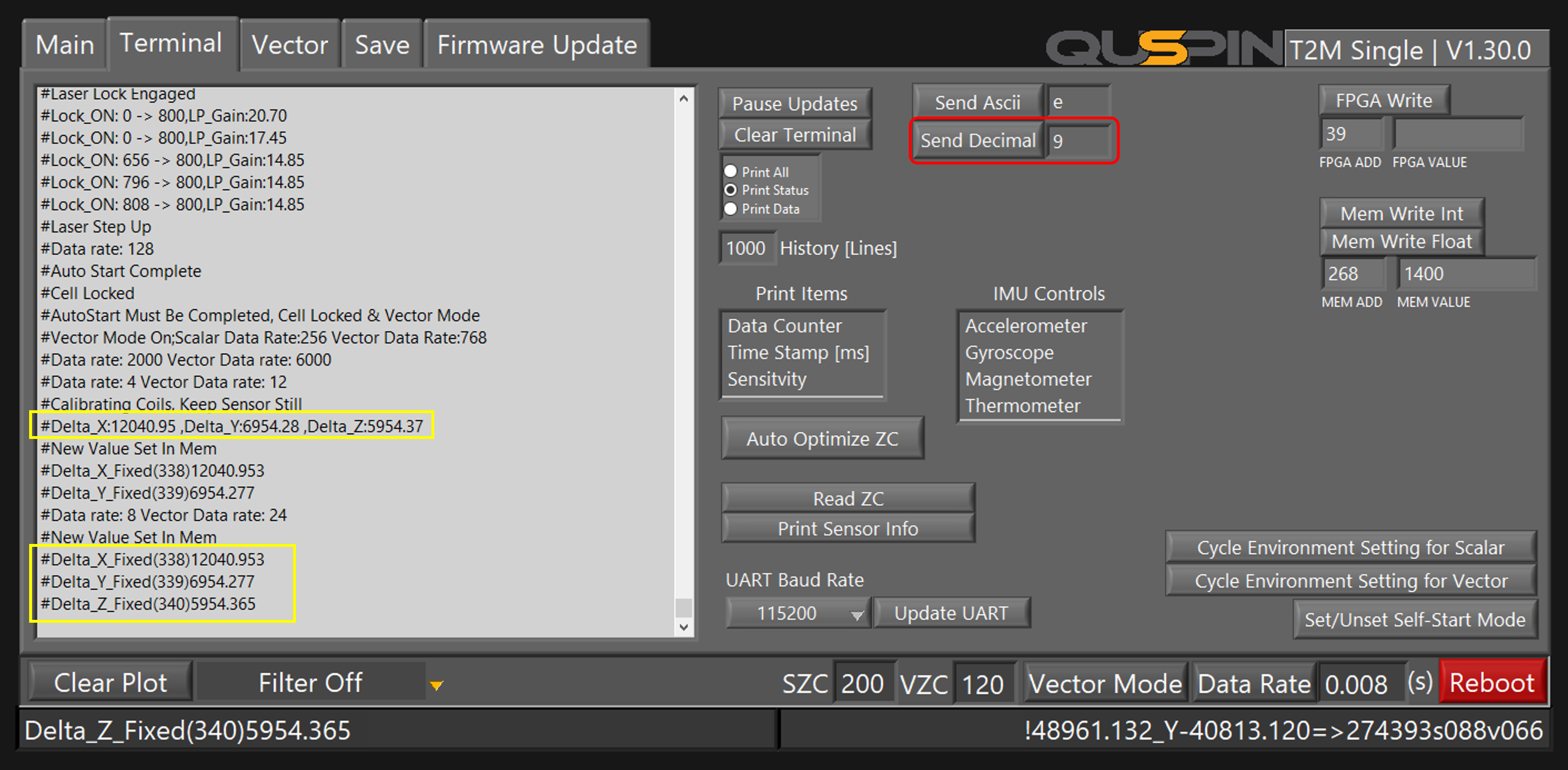
Conclusion: Benefits of Vector Coil Calibration
Following the streamlined steps outlined above, your Gen-2 QTFM sensor will be accurately calibrated for the vector coils. Calibration enables the use of the new Enhanced Vector Mode, introduced in firmware version V1_36 and later. This mode is the default setting when vector mode is enabled (#Vector_Mode: 0), and outputs vector data similarly to previous versions.
Advantages of Enhanced Vector Mode:
- Increased Tolerance to High-Frequency Noise: The Enhanced Vector Mode significantly improves the sensor’s ability to handle high-frequency noise, effectively increasing the bandwidth of each vector axis.
- Optimized for Magnetic Surveys: This mode is recommended for conducting magnetic surveys due to its enhanced sensitivity and noise tolerance.
Consideration:
- Initial Drift in Cold Start: One drawback of the new vector mode is that the sensor may experience drift for about 5 minutes when cold-started.
Hardware Update and Optional Modifications for Improving Vector Performance
New Vector Electronics Hardware:
- Increased Sensitivity and Drift Reduction: Soon, new vector electronics hardware will be commercially available, further enhancing the vector sensor’s sensitivity and eliminating low-frequency drift.
DIY Modification for Enhanced Performance:
- ECU Board Modification: In the interim, the top ECU board (vector electronics) can be modified to boost sensitivity and high-frequency tolerance.
- Resistor Replacement: Replace the 0603 resistors on the top ECU board with resistors in the range of 150-220 ohms. See the Picture below for the resistor location.
- Post-Modification Calibration: After this modification, it is crucial to recalibrate the vector coils to ensure optimal performance.
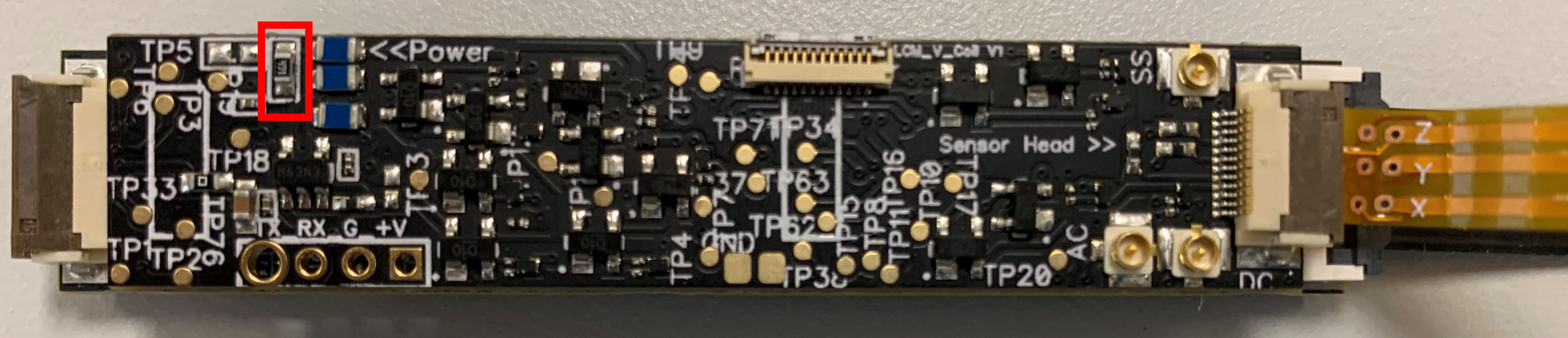